Project Overview
The PacBots team embarked on a challenging journey to create a micro-mouse-style robot capable of fast, efficient field navigation. With clear goals focused on speed, stability, and optimization, we applied creative thinking and precision engineering to build a platform that could adapt dynamically to competition environments.
Through a combination of research, prototyping, and testing, we moved beyond basic designs and crafted a uniquely effective robot that reflects both innovation and technical skill. This project solidified key foundations in mechanical systems, sensor integration, and iterative development methodologies.
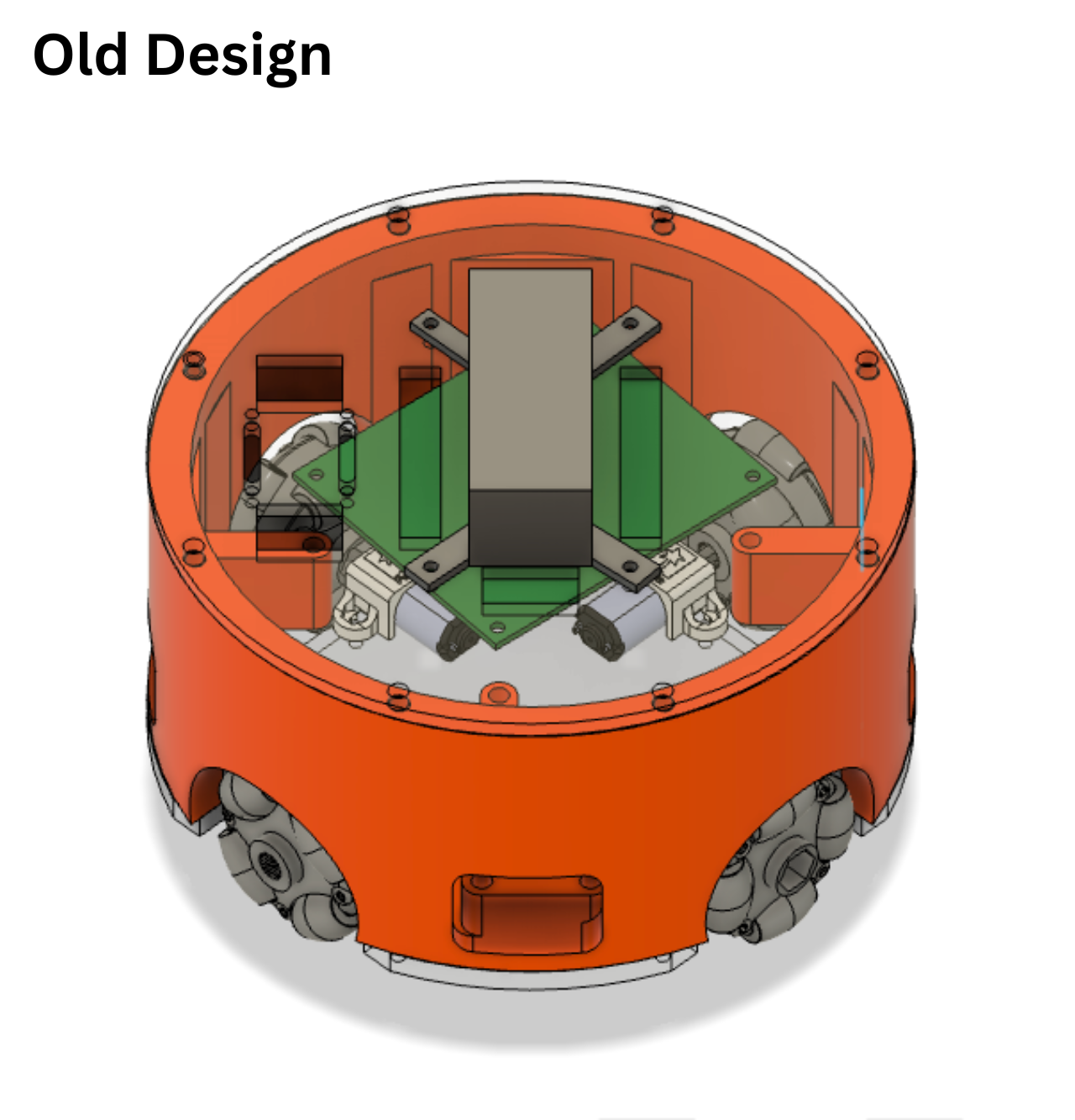
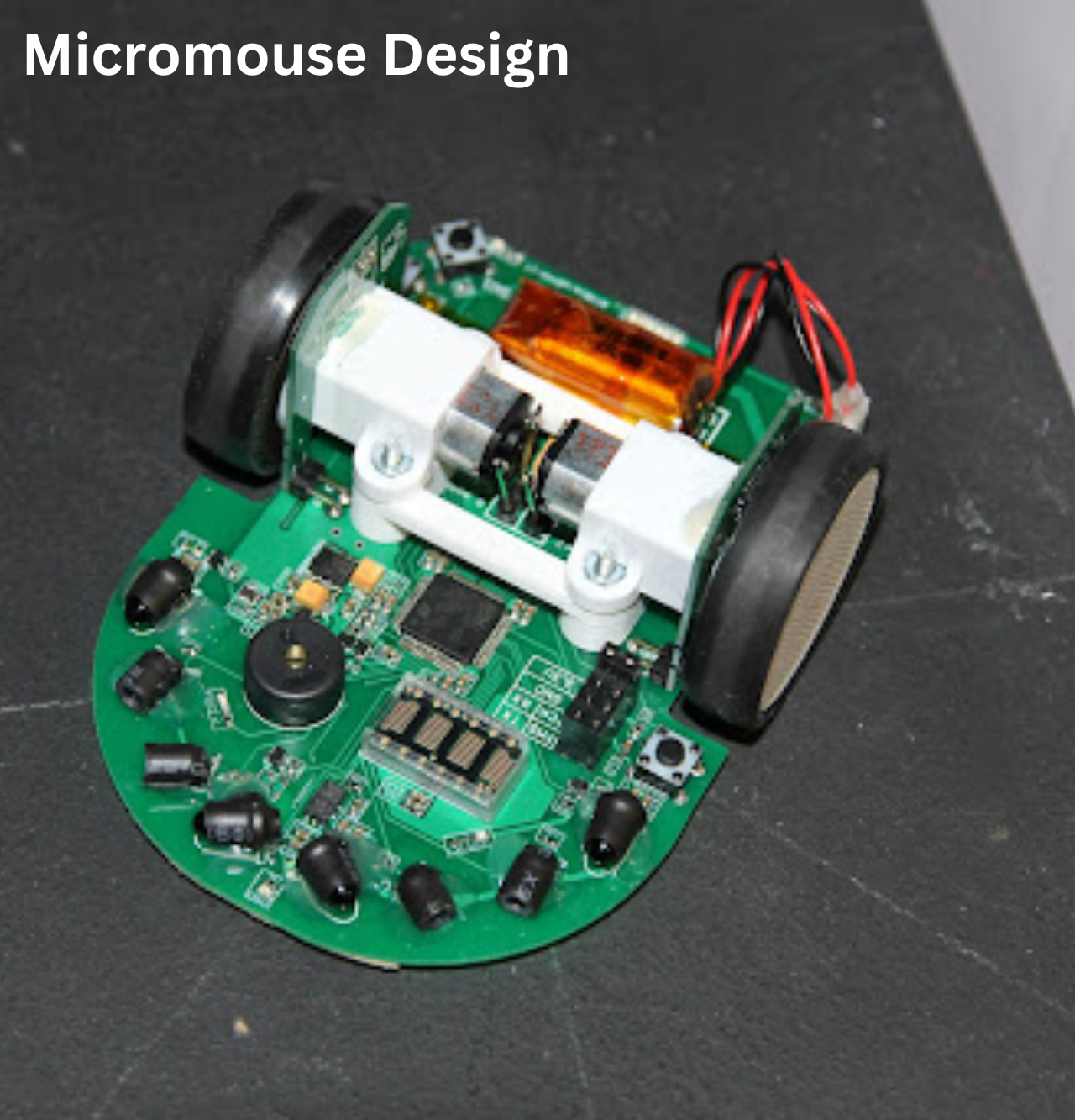
Design Evolution and Brainstorming
We initiated the semester with deep brainstorming sessions, analyzing the pros and cons of various drive and chassis setups. Early ideas revolved around two-wheel balancing systems supplemented by ball casters; however, simulations and small-scale mockups revealed stability issues under quick acceleration or sharp turns.
Consequently, we transitioned to a four-wheel design, supported by a mid-mounted gearing system that evenly distributed torque and minimized tipping risk. These changes were supported by careful placement of ToF sensors to ensure maximum obstacle detection with minimal blind spots.
CAD Models and Engineering Drawings
Our CAD work served as the digital backbone of the entire project. Early models captured the overall spatial layout, highlighting critical interactions between motors, gears, wheels, and PCBs. These models allowed us to predict mechanical stresses and adjust dimensions well before any material was cut or printed.
Final engineering drawings provided detailed visualizations, including clear tolerances, fastener types, and key alignments. The seamless collaboration between mechanical and electronics teams began with these CAD models, ensuring no collision or interference among subsystems during final assembly.
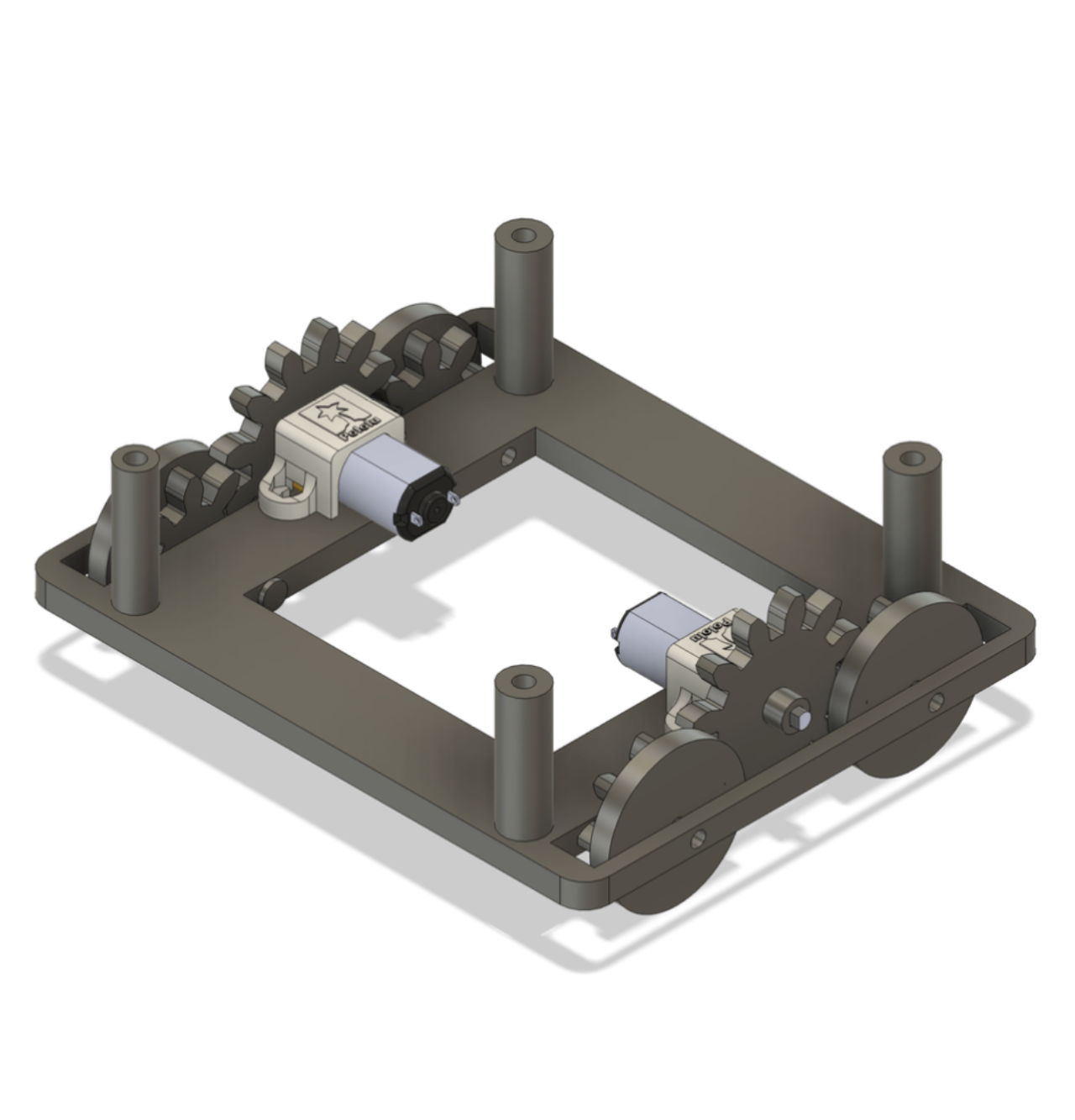
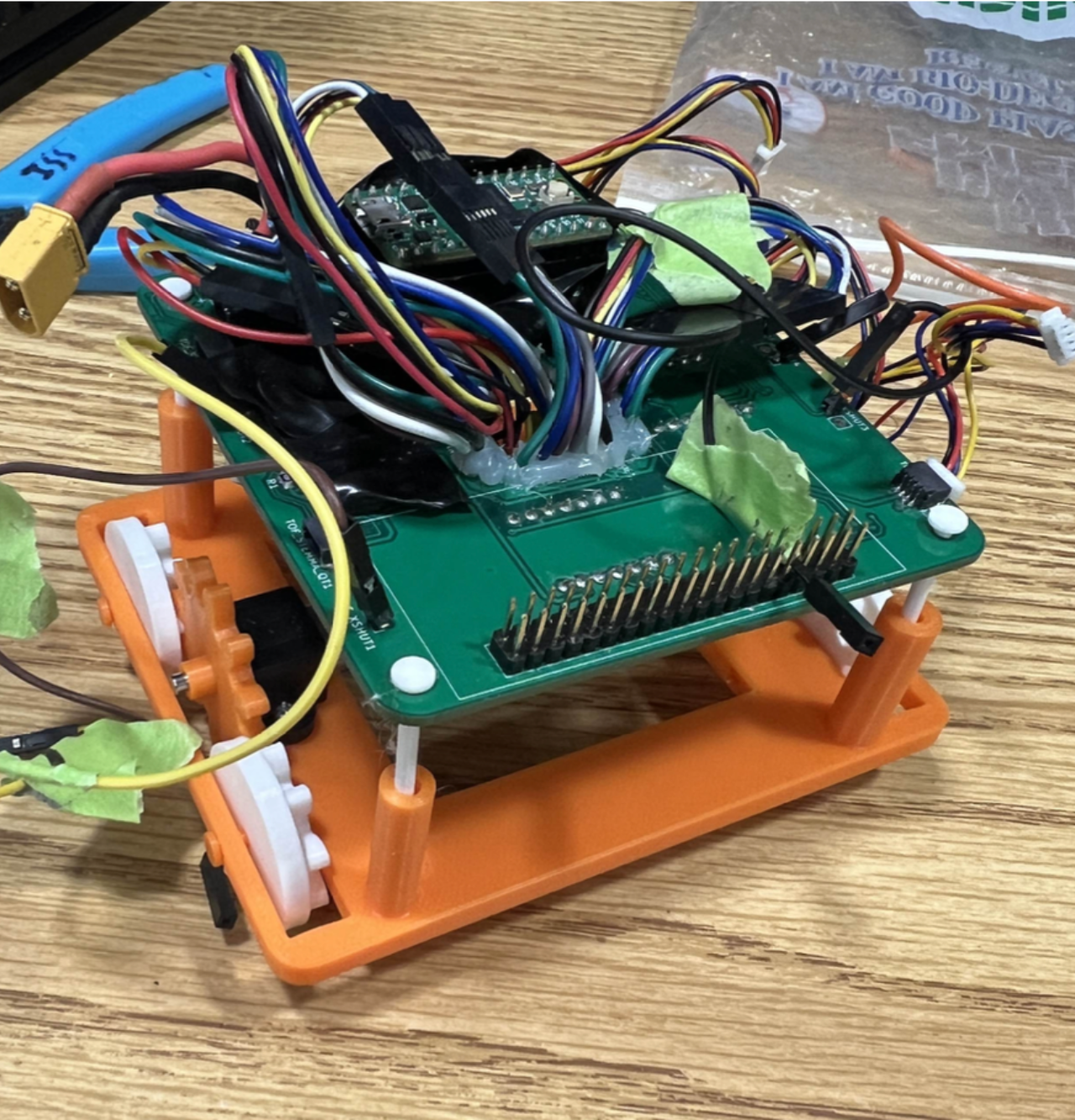
Design Pivot and Redesign
As testing proceeded, it became clear that a gear-driven drivetrain introduced unwanted backlash at high speeds. Recognizing this risk, we pivoted to a belt-driven system that enabled smoother, more continuous torque transmission with lower mechanical noise and improved reliability.
Additionally, significant structural revisions such as lowering the center of gravity by moving sensors underneath and stacking the battery beneath the PCB helped optimize space and stability. Multiple design iterations were physically prototyped and field-tested for validation before final integration.
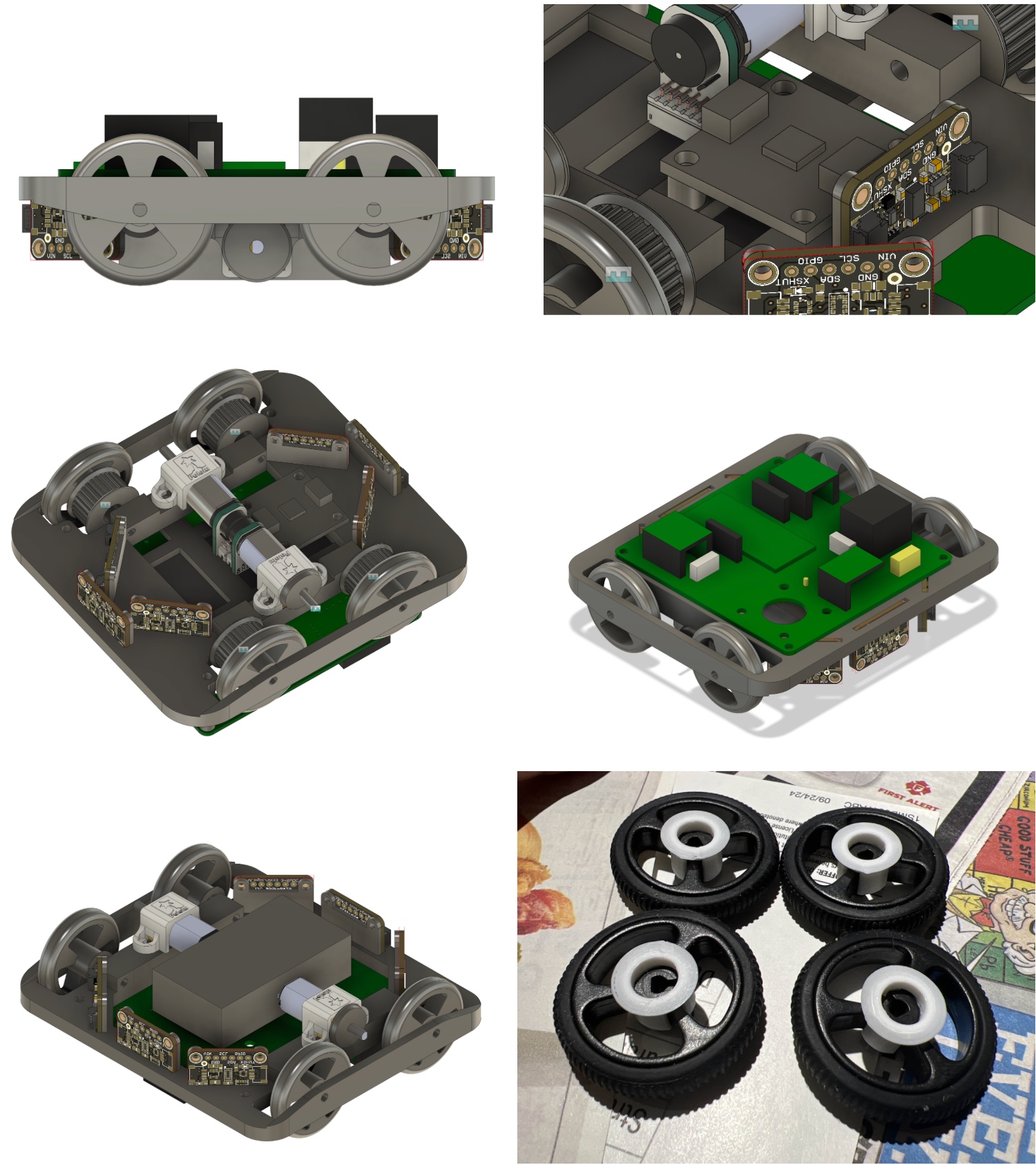
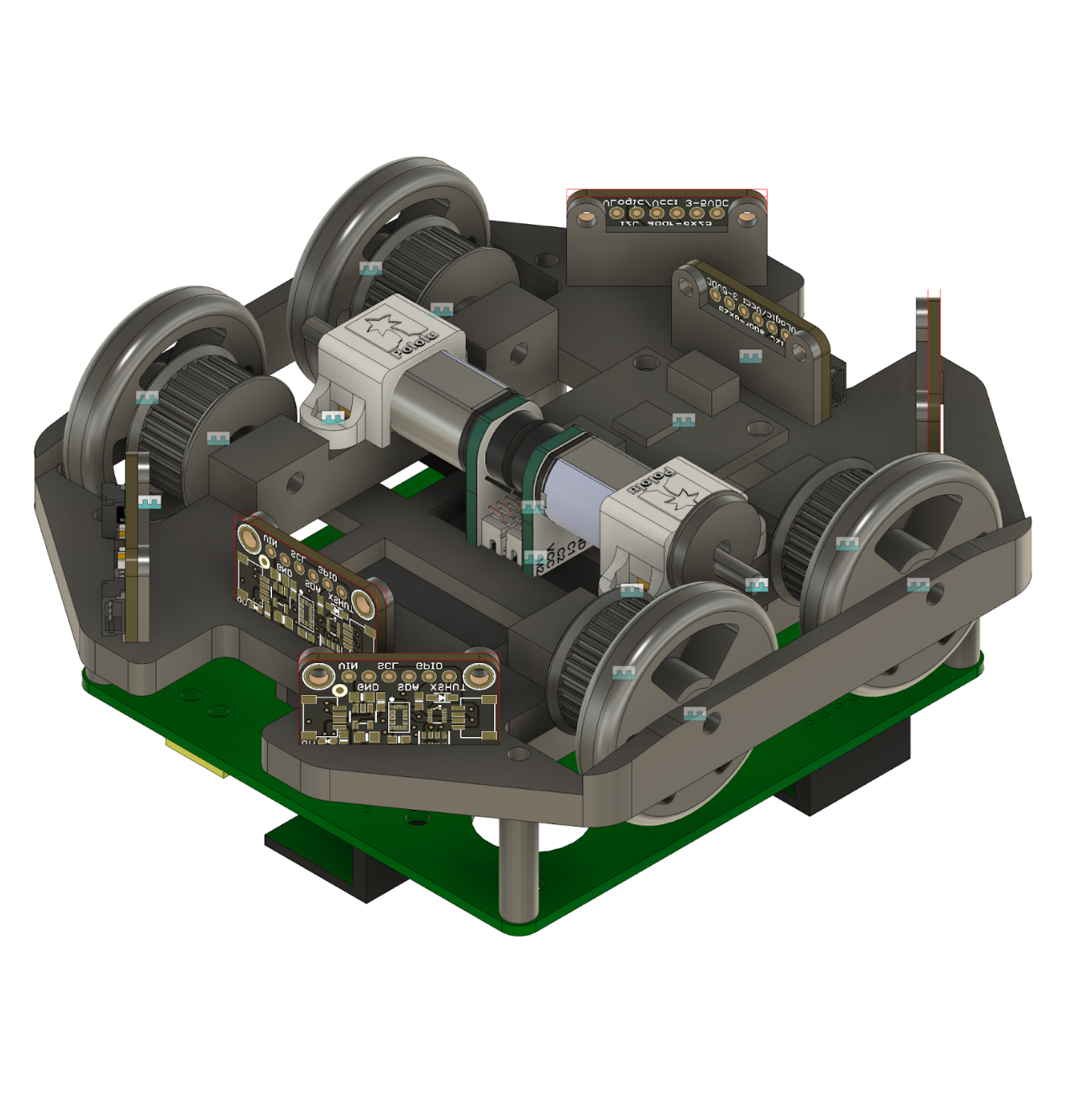
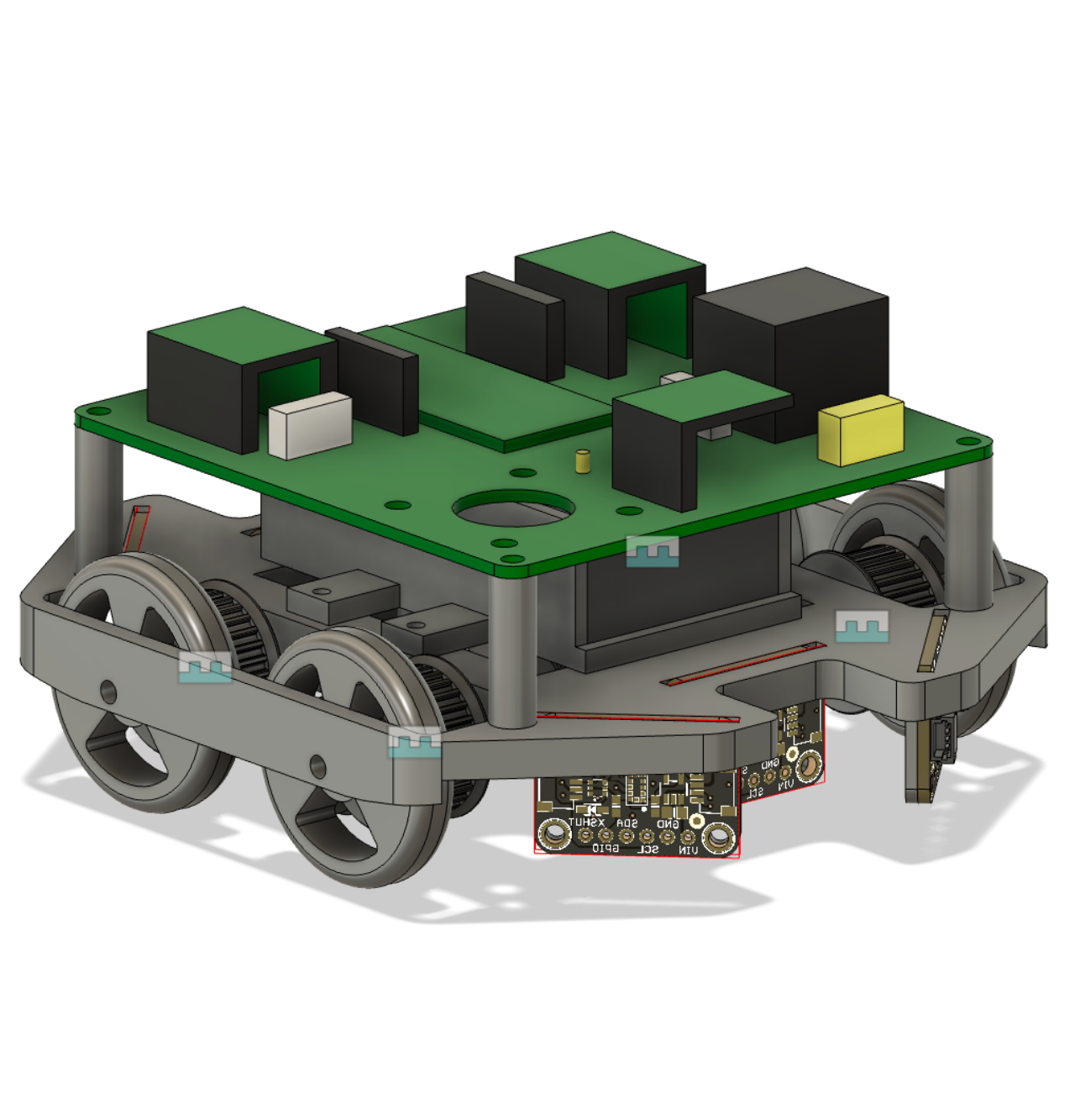
Aesthetic and Functional Arena Design
Beyond the robot, we tackled field infrastructure as well. Using CNC techniques, wood cutting, and precision painting, we manufactured a complete competition arena that matched regulation specifications. Surface smoothness and dimensional accuracy were prioritized to simulate real competition conditions accurately.
Creative use of recycled components from earlier years helped reduce waste and costs. Assembling the arena also sharpened our large-scale fabrication, material handling, and teamwork skills under tight deadlines.
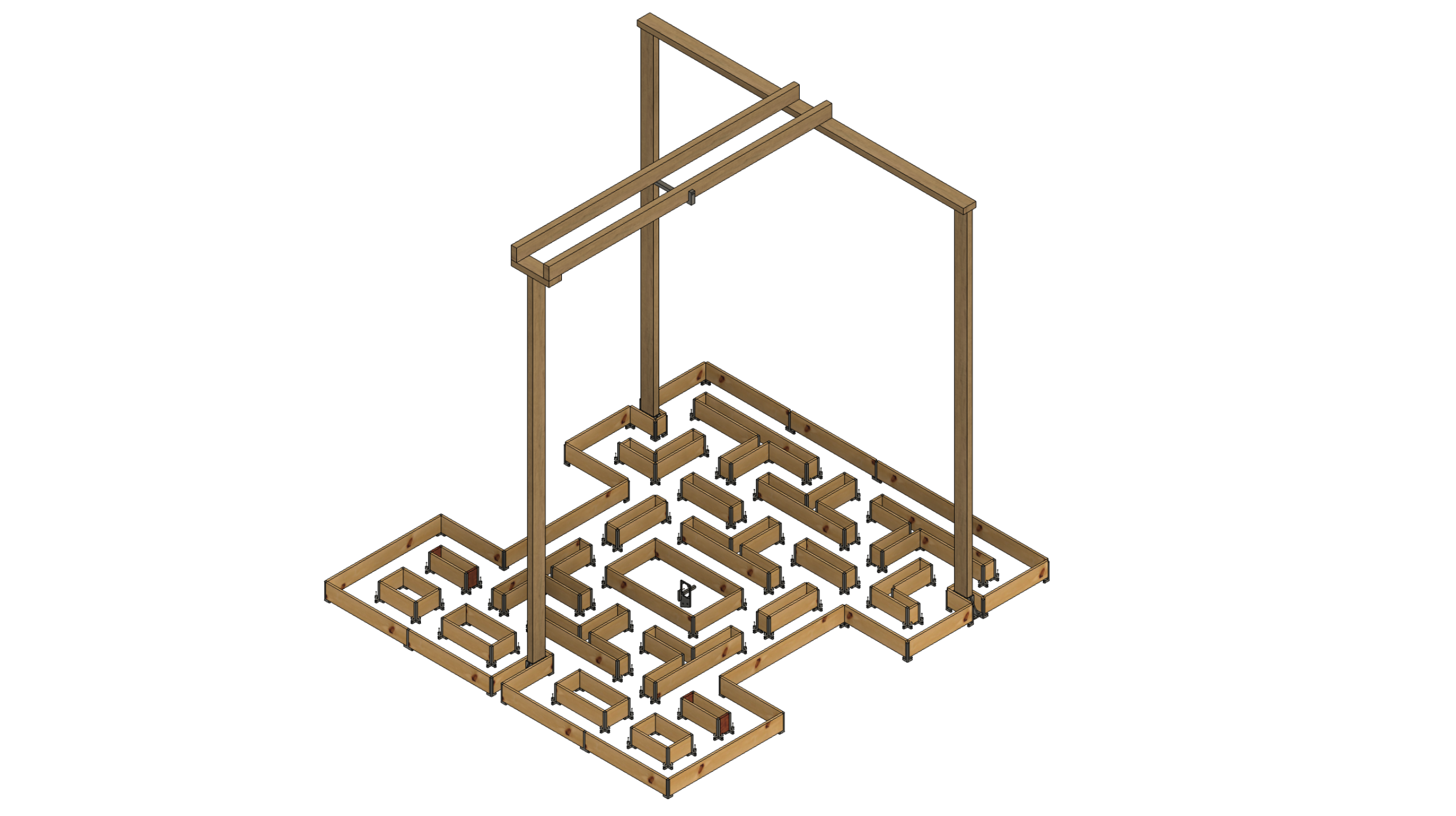
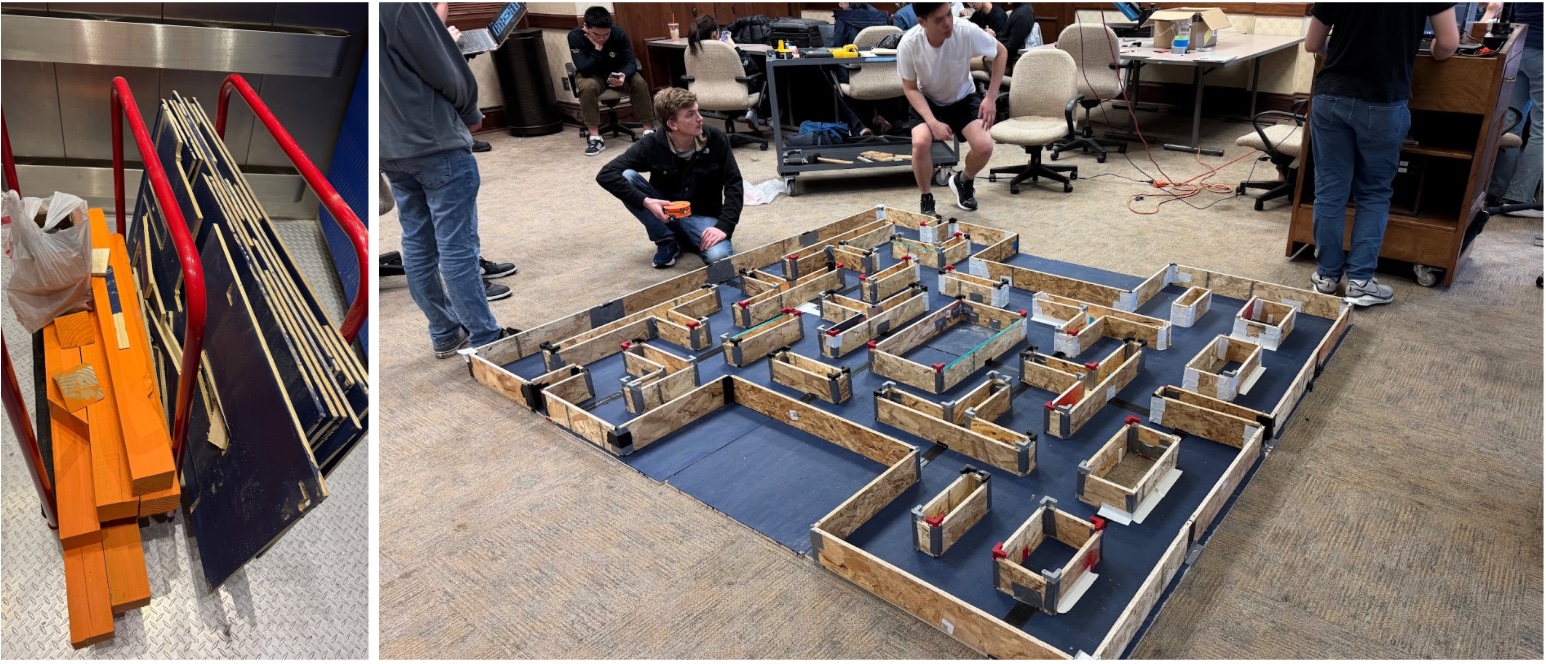
Trophy Design and Fabrication
In a fun cross-disciplinary twist, we designed Pac-Man themed competition trophies. The first-place trophy mirrored Pac-Man himself, while second and third place were stylized as blue ghosts, all fabricated from a mix of 3D-printed bases and precision laser-cut Delrin layers for enhanced durability and a professional finish.
This experience broadened our creative design horizons and gave valuable exposure to branding, theming, and aesthetic engineering beyond pure functionality.
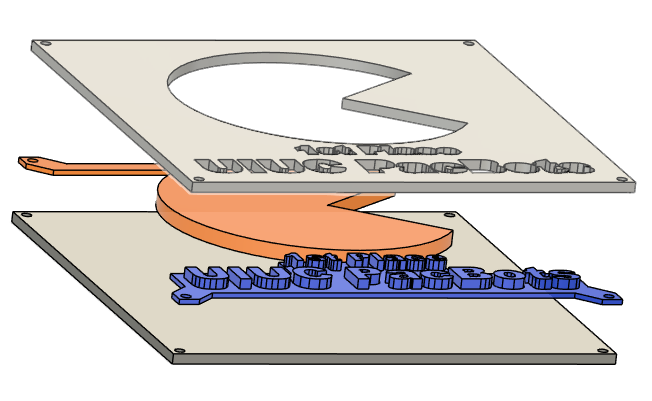
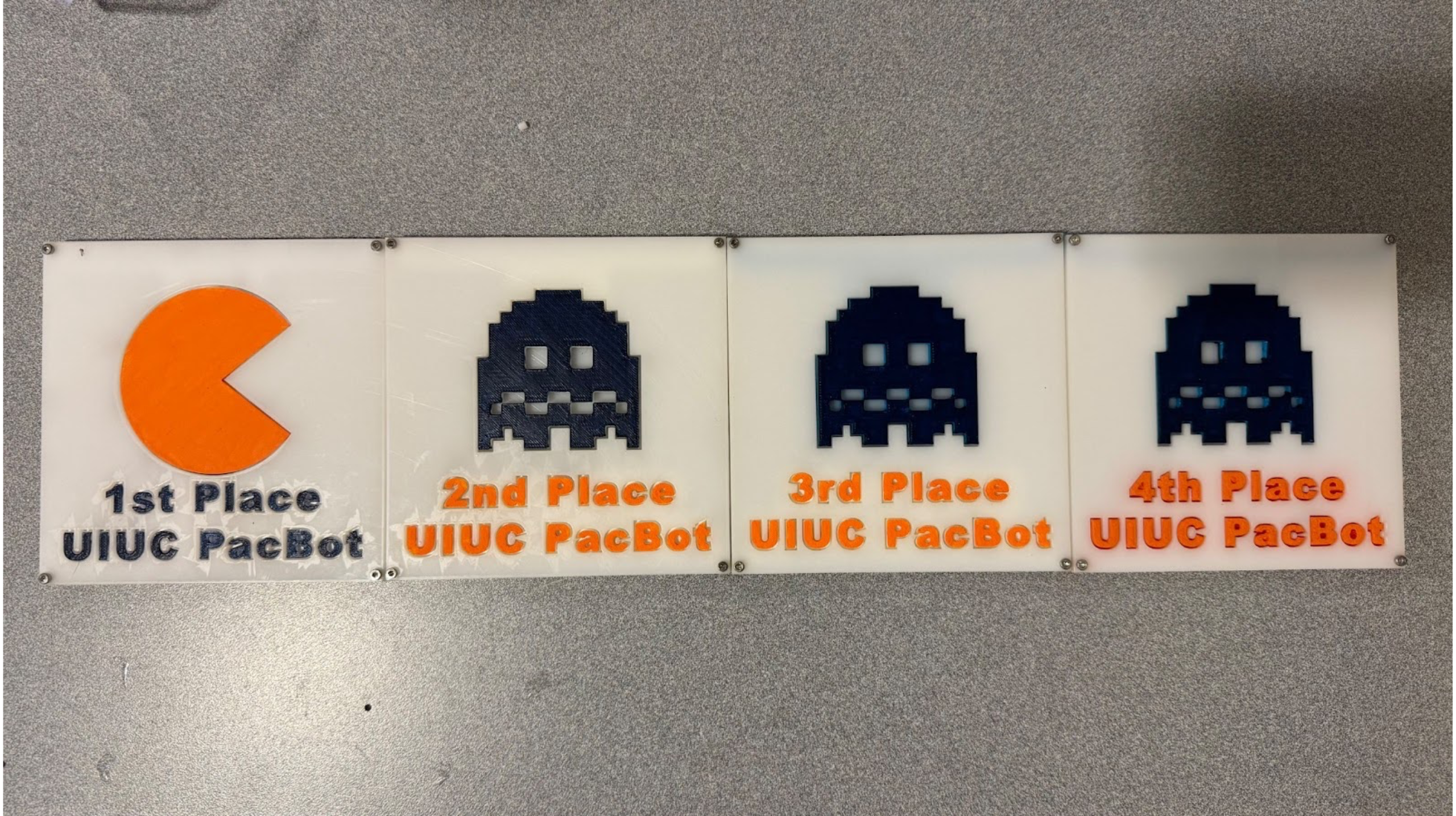
Results and Reflections
Our journey through PacBots strengthened not just our engineering abilities but also our creativity, resilience, and collaboration. This project underscored the importance of prototyping fast, failing early, and constantly learning from real-world feedback. We leave this semester better equipped to tackle larger, more ambitious challenges ahead.
The technical progress achieved — from advanced mechanical designs to functional system integration — sets a strong precedent for future improvements, and we look forward to building even more competitive and innovative robots next season.